Ok so I lied, I said I’d be back when the rain stopped but haven’t written an update for 5 weeks.
Where shall I start? The project is still not finished but an end is in sight. After the last post, I built the roof frame and managed to lift the roof into place on my own. I figured if the ancient Egyptians could build pyramids I could lift a roof. I’d be lying (again) if I said it was easy. A steel roof 10′ x 10′ with a wooden frame weighs … well lots, and lifting it into place required me placing wooden rails either side and physically lifting the roof past the tipping point to allow it to fall into place. I stopped for a breather after that!
With the roof in place I was able to complete the walls and fascia boards and move onto the rear rail assembly that will support the roof in a “rolled-off” position. Digging 2′ holes for the fence posts was easy enough, trying to hold a post upright and level whilst aligning it with the roof rail (which I couldn’t see) proved to be to too difficult and I eventually built the whole rear assembly upside down on the lawn. After my Herculean efforts with the roof I asked my brother to lend a hand to carry this into place. With a lawn that slopes making everything square and upright was a task. I propped the ends of the main framework on timbers to get it level before fixing the upright fence posts in place. A slight error on my part means one of the posts is not perfectly upright – but close enough. The photo makes it look worse than it is because the steel cladding on the shed runs out slightly where the fascia board pulls the top in. No really – I’m not making excuses.
So where are we – roof in place – rear assembly in place – oh I know what I missed: After getting the roof in place the heavens opened and it rained like I should have built an Ark not an observatory! To my horror the roof leaked. The only reason for buying the steel shed was to make sure the structure was weather proof! Ahhhh. I spent an afternoon with buckets and silicone sealant trying to make running repairs but the silicone washed out but luckily the buckets kept the floor from getting any wetter than it was. The floor wasn’t sealed, it’s made of a type of board that isn’t weather proof and the damp barrier was under it, so when the boards got wet I did worry a little. After several attempts to repair the leaks I got my brother over to help lift the roof off – the once heavy roof was now even heavier as the rails and cross supports where now in place! In hind-sight it was a 4 man job, but by the time we realised that we were past the point of no return. We stripped the roof boards off and re-assembled them, this time with a thick layer of black sticky roof repair goo between each joint and in all the screw holes. On either end we used roofing bolts instead of the provided screws and washers (these are self-tapping bolts with a built in fibre washer). Black goo oozing from the screw holes was dismissed as a necessary evil and the rebuilt structure was manhandled into place, now all I needed was rain to test it.
As luck would have it I didn’t have to wait too long and again AHHHH it leaked! Only in two places, 1 was a screw hole, the other a seam between 2 of the roof sheets. I fixed the screw hole by removing the screw and putting enough black goo over the hole to plug 20 holes, but better safe than sorry. The seam was another issue. The problem was where the sheets overlap. I ran a bead of goo down the whole length of the seam and screwed through from the inside – pulling the two sheets together with goo squeezing out both sides.
So the roof is on, the rear frame in place – no leaks? still waiting for significant rain to test it – on to the wheels and rails. Running castors on a wooden beam will quickly wear a groove, I decided to buy some steel channel for the castors to run in. I decided 4 castors each side would be enough – and if not I’d put some more on. Not exactly a scientific approach – but it worked. So how do you screw castors to a rail that’s upside down and weighed down with a roof. I have these clamps that work by pulling on a trigger to close them and pressing a release button to unclamp. by removing one end of the clamp and putting it on the other end it becomes a spreader! I used these to lift and hold the roof with wooden blocks just in case the roof fell while my arms were under it! The steel was easy to work and I drilled and counter sunk the holes until I broke my counter sink bit, then I used the 20mm bit I’d used on the brake disk as a counter sink – that was fine. Rails in place, wheels in place – paint applied to all exposed steel – now it’s taking shape. Before the wheels and steel rails I was able to haul the roof back a few feet, but now I was able to run it fully off with one hand!
Exterior timber has been painted with wood preserver and the floor covered with wood-oil to waterproof it. I’ve built a wide shelf along the back wall to hold a laptop and any other bits and pieces. I’ve also run an armoured power cable the length of the garden and wired up a consumer unit with RCD and 4 x 13amp power sockets. I have a 6amp circuit for lighting but don’t have a light yet!
So here’s a few photos:
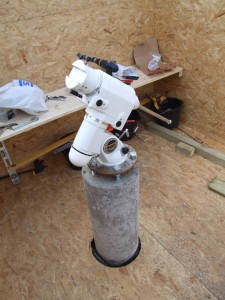
|
Here’s a shot of the mount in place. I tried it to make sure it pointed north but the clouds came over before nightfall so I couldn’t get a sighting on polaris. I’m happy there’s enough adjustment to get it aligned, even if the pier alignment is off. |
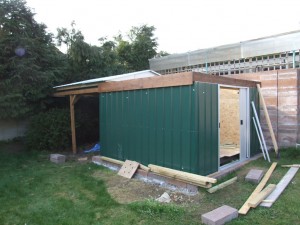
|
Here’s a shot of the observatory (careful not to call it a shed!) with the roof off. Construction still taking place so it still looks like a building site. |
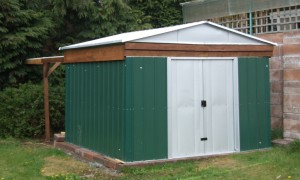
|
Here’s the latest shot of the outside of the observatory. |
|
The locking mechanism. Likely to be a temporary solution while I look for something more permanent. The clamp stops the roof rolling off and also keeps it down. I’ve also added some other clamps and locks to keep it all secure. |
|
Here’s a panorama of the inside of the shed at eye-level. It shows castors, rails, clamps and black goo if you look hard enough 
|
Update 19:05 25-04-2010:
I’m done! I painted the pier and the brake disk, installed a power-line Ethernet adapter to give me network access and fitted a second hasp to the door. I bought 2 padlocks and fitted them as well as some other bits and pieces to help secure the structure.
All that’s left is to find a spanner that will fit under the brake disk to tighten the centre bolt that holds the mount in place. Nothing too serious but without this simple tool I can’t do any more. When done up the bolt is slightly recessed into the brake disk making it difficult to get any type of adjustable spanner (wrench) in there. It’s cloudy tonight so no rush – you can be sure it’ll rain for the next 2 weeks!
Hopefully the next post will be first light at Ty Du Observatory.
Watch this space … 
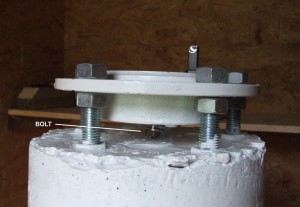